Материал | Коэффициент линейного теплового расширения | |
10-6 °С-1 | 10-6 °F-1 | |
ABS (акрилонитрил-бутадиен-стирол) термопласт | 73.8 | 41 |
ABS — стекло, армированное волокнами | 30.4 | 17 |
Акриловый материал, прессованный | 234 | 130 |
Алмаз | 1.1 | 0.6 |
Алмаз технический | 1.2 | 0.67 |
Алюминий | 22.2 | 12.3 |
Ацеталь | 106.5 | 59.2 |
Ацеталь , армированный стекловолокном | 39.4 | 22 |
Ацетат целлюлозы (CA) | 130 | 72.2 |
Ацетат бутират целлюлозы (CAB) | 25.![]() | 14 |
Барий | 20.6 | 11.4 |
Бериллий | 11.5 | 6.4 |
Бериллиево-медный сплав (Cu 75, Be 25) | 16.7 | 9.3 |
Бетон | 14.5 | 8.0 |
Бетонные структуры | 9.8 | 5.5 |
Бронза | 18.0 | 10.0 |
Ванадий | 8 | 4.5 |
Висмут | 13 | 7.3 |
Вольфрам | 4.3 | 2.4 |
Гадолиний | 9 | 5 |
Гафний | 5.9 | 3.3 |
Германий | 6.1 | 3.4 |
Гольмий | 11.2 | 6.2 |
Гранит | 7.9 | 4.4 |
Графит, чистый | 7.9 | 4.4 |
Диспрозий | 9.9 | 5.5 |
Древесина, пихта, ель | 3.7 | 2.1 |
Древесина дуба, параллельно волокнам | 4.![]() | 2.7 |
Древесина дуба , перпендикулярно волокнам | 5.4 | 3.0 |
Древесина, сосна | 5 | 2.8 |
Европий | 35 | 19.4 |
Железо, чистое | 12.0 | 6.7 |
Железо, литое | 10.4 | 5.9 |
Железо, кованое | 11.3 | 6.3 |
Золото | 14.2 | 8.2 |
Известняк | 8 | 4.4 |
Инвар (сплав железа с никелем) | 1.5 | 0.8 |
Инконель (сплав) | 12.6 | 7.0 |
Иридий | 6.4 | 3.6 |
Иттербий | 26.3 | 14.6 |
Иттрий | 10.6 | 5.9 |
Кадмий | 30 | 16.8 |
Калий | 83 | 46.1 — 46.4 |
Кальций | 22.3 | 12.4 |
Каменная кладка | 4.7 — 9.![]() | 2.6 — 5.0 |
Каучук, твердый | 77 | 42.8 |
Кварц | 0.77 — 1.4 | 0.43 — 0.79 |
Керамическая плитка (черепица) | 5.9 | 3.3 |
Кирпич | 5.5 | 3.1 |
Кобальт | 12 | 6.7 |
Констанан (сплав) | 18.8 | 10.4 |
Корунд, спеченный | 6.5 | 3.6 |
Кремний | 5.1 | 2.8 |
Лантан | 12.1 | 6.7 |
Латунь | 10.4 | |
Лед | 51 | 28.3 |
Литий | 46 | 25.6 |
Литая стальная решетка | 10.8 | 6.0 |
Лютеций | 9.9 | 5.5 |
Литой лист из акрилового пластика | 81 | 45 |
Магний | 25 | 14 |
Марганец | 22 | 12.3 |
Медноникелевый сплав 30% | 16.![]() | 9 |
Медь | 16.6 | 9.3 |
Молибден | 5 | 2.8 |
Монель-металл (никелево-медный сплав) | 13.5 | 7.5 |
Мрамор | 5.5 — 14.1 | 3.1 — 7.9 |
Мыльный камень (стеатит) | 8.5 | 4.7 |
Мышьяк | 4.7 | 2.6 |
Натрий | 70 | 39.1 |
Нейлон, универсальный | 72 | 40 |
Нейлон, Тип 11 (Type 11) | 100 | 55.6 |
Нейлон, Тип 12 (Type 12) | 80.5 | 44.7 |
Нейлон литой , Тип 6 (Type 6) | 85 | 47.2 |
Нейлон, Тип 6/6 (Type 6/6), формовочный состав | 80 | 44.4 |
Неодим | 9.6 | 5.3 |
Никель | 13.0 | 7.2 |
Ниобий (Columbium) | 7 | 3.9 |
Нитрат целлюлозы (CN) | 100 | 55.![]() |
Окись алюминия | 5.4 | 3.0 |
Олово | 23.4 | 13.0 |
Осмий | 5 | 2.8 |
Палладий | 11.8 | 6.6 |
Песчаник | 11.6 | 6.5 |
Платина | 9.0 | 5.0 |
Плутоний | 54 | 30.2 |
Полиалломер | 91.5 | 50.8 |
Полиамид (PA) | 110 | 61.1 |
Поливинилхлорид (PVC) | 50.4 | 28 |
Поливинилденфторид (PVDF) | 127.8 | 71 |
Поликарбонат (PC) | 70.2 | 39 |
Поликарбонат — армированный стекловолокном | 21.5 | 12 |
Полипропилен — армированный стекловолокном | 32 | 18 |
Полистирол (PS) | 70 | 38.9 |
Полисульфон (PSO) | 55.8 | 31 |
Полиуретан (PUR), жесткий | 57.![]() | 32 |
Полифенилен — армированный стекловолокном | 35.8 | 20 |
Полифенилен (PP), ненасыщенный | 90.5 | 50.3 |
Полиэстер | 123.5 | 69 |
Полиэстер, армированный стекловолокном | 25 | 14 |
Полиэтилен (PE) | 200 | 111 |
Полиэтилен — терефталий (PET) | 59.4 | 33 |
Празеодимий | 6.7 | 3.7 |
Припой 50 — 50 | 24.0 | 13.4 |
Прометий | 11 | 6.1 |
Рений | 6.7 | 3.7 |
Родий | 8 | 4.5 |
Рутений | 9.1 | 5.1 |
Самарий | 12.7 | 7.1 |
Свинец | 28.0 | 15.1 |
Свинцово-оловянный сплав | 11.6 | 6.5 |
Селен | 3.8 | 2.1 |
Серебро | 19.![]() | 10.7 |
Скандий | 10.2 | 5.7 |
Слюда | 3 | 1.7 |
Сплав твердый (Hard alloy) K20 | 6 | 3.3 |
Сплав хастелой (Hastelloy) C | 11.3 | 6.3 |
Сталь | 13.0 | 7.3 |
Сталь нержавеющая аустенитная (304) | 17.3 | 9.6 |
Сталь нержавеющая аустенитная (310) | 14.4 | 8.0 |
Сталь нержавеющая аустенитная (316) | 16.0 | 8.9 |
Сталь нержавеющая ферритная (410) | 9.9 | 5.5 |
Стекло витринное (зеркальное, листовое) | 9.0 | 5.0 |
Стекло пирекс, пирекс | 4.0 | 2.2 |
Стекло тугоплавкое | 5.9 | 3.3 |
Строительный (известковый) раствор | 7.3 — 13.5 | 4.1-7.5 |
Стронций | 22.5 | 12.5 |
Сурьма | 10.![]() | 5.8 |
Таллий | 29.9 | 16.6 |
Тантал | 6.5 | 3.6 |
Теллур | 36.9 | 20.5 |
Тербий | 10.3 | 5.7 |
Титан | 8.6 | 4.8 |
Торий | 12 | 6.7 |
Тулий | 13.3 | 7.4 |
Уран | 13.9 | 7.7 |
Фарфор | 3.6-4.5 | 2.0-2.5 |
Фенольно-альдегидный полимер без добавок | 80 | 44.4 |
Фторэтилен пропилен (FEP) | 135 | 75 |
Хлорированный поливинилхлорид (CPVC) | 66.6 | 37 |
Хром | 6.2 | 3.4 |
Цемент | 10.0 | 6.0 |
Церий | 5.2 | 2.9 |
Цинк | 29.7 | 16.5 |
Цирконий | 5.7 | 3.2 |
Шифер | 10.![]() | 5.8 |
Штукатурка | 16.4 | 9.2 |
Эбонит | 76.6 | 42.8 |
Эпоксидная смола , литая резина и незаполненные продукты из них | 55 | 31 |
Эрбий | 12.2 | 6.8 |
Этилен винилацетат (EVA) | 180 | 100 |
Этилен и этилакрилат (EEA) | 205 | 113.9 |
Эфир виниловый | 16 — 22 | 8.7 — 12 |
Температура плавления серебра
Серебро —металл, способный стать жидким. Процесс плавки серебра является сложной задачей, требующей определенных знаний в этой сфере.
При недостаточной подготовки к плавлению металла есть вероятность получить серьезные ожоги или вызвать пожар. Помните, что плавить серебро рекомендуется на улице или в специализированном помещении.
Физические характеристики серебра
Несмотря на все свои преимущества, при взаимодействии с серой, находящейся в воздушном пространстве, серебро окисляется и покрывается налетом, что является причиной потемнения столовых приборов из серебра. Предлагаем Вам ознакомиться с особенностями металла:
- плавится серебро при 961,8 градусах, чтобы металл закипел стоит довести температуру до 2162 градусов;
- благодаря тому, что серебро хорошо отражает свет, оно становится популярным материалом для изготовления вещей и не требует особых усилий;
- из-за физико-химических свойств его используют в технической и роботостроительной промышленностях;
- плотность серебра на десять раз выше плотности воды.
При самостоятельной плавке металле следует знать его пробу, от пробы металла зависит температура плавления. Менее 90 % — температура плавки не более 780 градусов. Ювелирные мастера чаще всего пользуется в своей работе пробами 800 и 925.
Как расплавить серебро в домашних условиях
Приготовьте все инструменты и материалы, уделите внимание форме, в которую будет помещен жидкий металл после его плавки. Конечно, ее лучше купить в специализированном магазине, но есть вы решили смастерить ее самостоятельно, то пользуйтесь огнеупорными материалами. Например, гипса, кварцевого песка и пчелиного воска. Для плавки серебра в домашних условиях Вам понадобятся:
- слиток серебра,
- прочная металлическая ложка,
- горелка,
- щипцы с пинцетом,
- хризотиловый асбест,
- тетраборат натрия,
- форма, куда будет помещаться расплавленный металл.
Разложите удобно перечисленные выше материалы, наденьте плотную одежду, перчатки и защитные очки.
Процесс плавки серебра проходит в несколько этапов:
- Разрежьте лист хризотилового асбеста на четыре части, у вас должны получиться прямоугольники — один чуть меньше ложки, второй размером с ложку, остальные маленького размера.
- Чтобы в сплав не попал кислород, обработайте тетраборатом натрия (1:1) емкость, которую будете использовать при плавлении металла. Доведите тетраборат натрия до густой смеси темно-зеленого оттенка.
- Затем поместите в ёмкость кусок металла и дождитесь времени, когда металл начнет плавиться.
- Проверьте наличие блеска у жидкого серебра, если блеск отсутствует, то следует повторить процесс еще раз.
Если Вы хотите придать сплаву форму, то сразу же после плавки перелейте его в выбранную форму, вовремя процедуры пользуйтесь щипцами и пинцетом во избежание ожогов, дождитесь загустения, поместите в воду. Если серебряное изделие не отошло от формы, отделите его руками.
Материалы для 3D печати — пластик, фотополимер, гипс, полиамид
Нейлон (Nylon) – это одно из популярных семейств синтетических полимеров, используемых в различных производствах. В области 3Д-печати этот материал воспринимается своеобразным тяжеловесом. Если сравнивать этот материал с другими, то у него более сбалансированные показатели гибкости, жесткости и долговечности. Особым качеством Nylon считается возможность окрашивания материала как до, так и после 3Д-печати. Этот материал отличается по маркам, но в 3Д-печати, как правило, используются 618 и 645 Nylon.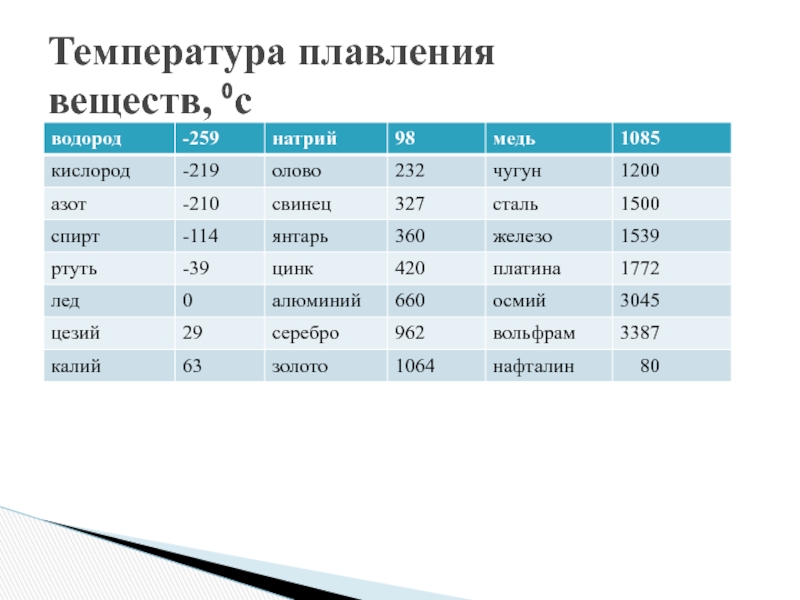
Что печатают из Nylon?
Нейлон в 3Д-печати получил такое же широкое применение как и в промышленной сфере. Учитывая его гибкость, длительный срок службы, а также жесткость материала, его используют для 3Д-печати функциональных прототипов, разнообразных механических узлов и деталей, к примеру, зубчатых колес. Применяют Nylon для печати разнообразных инструментов, в том числе и медицинских. В целом данный материал отличается высокой универсальностью и применим для решения самого широкого круга задач. А в силу того, что Nylon характеризуется очень низким коэффициентом трения, то это идеальный вариант для 3Д-печати движущихся деталей. Например, можно напечатать втулку для вращающейся на низких оборотах оси, в местах не неприменим подшипник, или шестеренок, не нуждающихся в смазывании.
У нейлона высокий показатель прочности на разрыв, благодаря чему из него печатаются крепежные элементы в виде хомутов и канатов. Недостаток нейлона заключается в гигроскопичности. Этот материал способен впитать за сутки воды в массе до 10% от собственного веса, хотя во многом это будет зависеть от сорта используемого нейлона.
Технические характеристики Nylon
Материал характеризуется высокой прочностью и гибкостью, а также очень длительным сроком эксплуатации. Кроме того Nylon является безопасным материалом с экологической точки зрения, характеризуется приемлемыми показателями термоусадки и деформации. Помимо этого Nylon обладает следующими техническими характеристиками:
Температура стеклования 49,4-68,2°C
Температура плавления 2014-218°C
Плотность 1,134 г/см3
Влагопоглощение 3,09%
Прочность на разрыв 65,99МПа
Относительное удлинение при разрыве более300%
Также нейлон характеризуется стойкостью к любым органическим растворителям, эластичностью и износостойкостью. Но при пиролизе этот материал способен выделять токсичные пары. Окрашивание материала возможно при помощи кислотных красителей.
ICSC 1215 — ГИПС (МИНЕРАЛ)
ICSC 1215 — ГИПС (МИНЕРАЛ)ГИПС (МИНЕРАЛЬНЫЙ) | ICSC: 1215 (ноябрь 2009 г.![]() |
Дигидрат сульфата кальция |
ОСТРЫЕ ОПАСНОСТИ | ПРЕДУПРЕЖДЕНИЕ | ПОЖАРОТУШЕНИЕ | |
---|---|---|---|
ПОЖАР И ВЗРЫВ | Не горючий.При пожаре выделяет раздражающие или токсичные пары (или газы). | В случае возгорания поблизости используйте соответствующие средства пожаротушения. |
СИМПТОМЫ | ПРЕДУПРЕЖДЕНИЕ | ПЕРВАЯ ПОМОЩЬ | |
---|---|---|---|
Вдыхание | Кашель. | Используйте местную защиту от выхлопных газов или дыхательных путей. | Свежий воздух, отдых. |
Кожа | Промойте, а затем вымойте кожу водой с мылом.![]() | ||
Глаза | Покраснение. Боль. | Носите защитные очки. | Сначала промыть большим количеством воды в течение нескольких минут (снять контактные линзы, если это возможно), затем обратиться за медицинской помощью. |
Проглатывание | Не есть, не пить и не курить во время работы. | Прополоскать рот. |
ЛИКВИДАЦИЯ УТЕЧЕК | КЛАССИФИКАЦИЯ И МАРКИРОВКА |
---|---|
Средства индивидуальной защиты: респиратор с фильтром твердых частиц, адаптированный к концентрации вещества в воздухе. Смести просыпанное вещество в закрытые контейнеры. При необходимости сначала увлажните, чтобы предотвратить запыление. | В соответствии с критериями СГС ООН Транспорт |
ХРАНЕНИЕ | |
УПАКОВКА | |
Подготовлено международной группой экспертов от имени МОТ и ВОЗ,
при финансовой поддержке Европейской комиссии. |
ГИПС (МИНЕРАЛ) | КМГС: 1215 |
ФИЗИЧЕСКАЯ И ХИМИЧЕСКАЯ ИНФОРМАЦИЯ | |
---|---|
Физическое состояние; Внешний вид Физические опасности Химическая опасность | Формула: CaSO 4 .2Н 2 О |
ВОЗДЕЙСТВИЕ И ВЛИЯНИЕ НА ЗДОРОВЬЕ | |
---|---|
Пути воздействия Последствия кратковременного воздействия | Риск вдыхания Последствия длительного или многократного воздействия |
ПРЕДЕЛЫ ВОЗДЕЙСТВИЯ НА РАБОЧЕМ МЕСТЕ |
---|
TLV: (вдыхаемая фракция): 10 мг/м 3 , как TWA. МАК: (вдыхаемая фракция): 4 мг/м 3 ; группа риска по беременности: C. МАК: (вдыхаемая фракция): 1,5 мг/м 3 ; группа риска по беременности: C |
ПРИМЕЧАНИЯ |
---|
Гипс является природной формой продукта и может содержать кристаллический кремнезем.![]() Указана кажущаяся температура плавления, вызванная потерей кристаллической воды. См. ICSC 1589 и ICSC 1734. |
ДОПОЛНИТЕЛЬНАЯ ИНФОРМАЦИЯ |
---|
Классификация ЕС |
Все права защищены.Опубликованный материал распространяется без каких-либо явных или подразумеваемых гарантий. Ни МОТ, ни ВОЗ, ни Европейская комиссия не несут ответственности за интерпретацию и использование информации, содержащейся в этом материале. | |
Смотрите также: Токсикологические сокращения
Физическое состояние; Внешний вид БЕЛЫЙ КРИСТАЛЛИЧЕСКИЙ ПОРОШОК ИЛИ КОМКИ.Физические опасности Химические опасности | Формула: CaSO4.![]() Можно ли плавить гипс?К сожалению сернокислый кальций, гипс, CaSO4, удручающе стабилен и ничто несмертельное его не растворит .
Каковы 3 основные формы гипса? Будут обсуждаться три типа гипсовых изделий: гипс , камень и высокопрочный или улучшенный камень . Химически все три представляют собой полугидрат сульфата кальция. Как избавиться от гипса?4:2213:47Как снять гипсокартон со стены — YouTubeYouTube Что происходит с гипсом, когда он растворяется в почве? Напротив, гипс немедленно растворяется во влаге почвы, позволяя корням растений поглощать ионы кальция и сульфат-ионы. Поскольку он растворяется в почвенном растворе, гипс легко мигрирует в более низкие глубины почвы.
Что происходит с гипсом при нагревании на воздухе?При нагревании гипса на воздухе он теряет воду и сначала превращается в полугидрат сульфата кальция (бассанит, часто называемый просто «гипсом»), а при дальнейшем нагревании — в безводный сульфат кальция (ангидрит). В чем разница между известняком и гипсом в почве?Известняк не мигрирует в почву и эффективен только на глубину внесения. Напротив, гипс немедленно растворяется во влаге почвы, позволяя корням растений поглощать ионы кальция и сульфат-ионы. Поскольку он растворяется в почвенном растворе, гипс легко мигрирует в более низкие глубины почвы. Какие минералы входят в состав гипса? Гипс представляет собой осадочную горную породу и кристаллический минерал.
⇐ Можно ли укладывать плитку выше 4-дюймового фартука? Как лак для волос удаляет чернила? ⇒ Похожие сообщения: |
Произошла ошибка при настройке пользовательского файла cookie
Этот сайт использует файлы cookie для повышения производительности.Если ваш браузер не принимает файлы cookie, вы не можете просматривать этот сайт.
Настройка браузера на прием файлов cookie
Существует множество причин, по которым файл cookie не может быть установлен правильно. Ниже приведены наиболее распространенные причины:
- В вашем браузере отключены файлы cookie. Вам необходимо сбросить настройки браузера, чтобы принять файлы cookie, или спросить вас, хотите ли вы принимать файлы cookie.
- Ваш браузер спрашивает, хотите ли вы принимать файлы cookie, и вы отказались.Чтобы принять файлы cookie с этого сайта, нажмите кнопку «Назад» и примите файл cookie.
- Ваш браузер не поддерживает файлы cookie. Попробуйте другой браузер, если вы подозреваете это.
- Дата на вашем компьютере в прошлом. Если часы вашего компьютера показывают дату до 1 января 1970 г., браузер автоматически забудет файл cookie. Чтобы это исправить, установите правильное время и дату на своем компьютере.
- Вы установили приложение, которое отслеживает или блокирует установку файлов cookie.Вы должны отключить приложение при входе в систему или проконсультироваться с системным администратором.
Почему этому сайту требуются файлы cookie?
Этот сайт использует файлы cookie для повышения производительности, запоминая, что вы вошли в систему, когда переходите со страницы на страницу. Предоставить доступ без файлов cookie потребует от сайта создания нового сеанса для каждой посещаемой вами страницы, что замедляет работу системы до неприемлемого уровня.
Что сохраняется в файле cookie?
Этот сайт не хранит ничего, кроме автоматически сгенерированного идентификатора сеанса в файле cookie; никакая другая информация не фиксируется.
Как правило, в файле cookie может храниться только информация, которую вы предоставляете, или выбор, который вы делаете при посещении веб-сайта. Например, сайт
не может определить ваше имя электронной почты, если вы не решите ввести его. Разрешение веб-сайту создавать файлы cookie не дает этому или любому другому сайту доступ к
остальной части вашего компьютера, и только сайт, создавший файл cookie, может его прочитать.
Гипсовый продукт – обзор
Мокрые скрубберы являются наиболее распространенным методом ДДГ, используемым в настоящее время, и включают в себя различные процессы, использование многих сорбентов и производятся большим количеством компаний.Сорбенты, используемые мокрыми скрубберами, включают сорбенты на основе кальция, магния, калия или натрия, аммиак или морскую воду. В настоящее время не используются коммерческие скрубберы на основе калия, а используется или демонстрируется лишь ограниченное количество систем аммиака или морской воды. Скрубберы на основе кальция, безусловно, являются наиболее популярными для производства электроэнергии, и эта технология обсуждается в этом разделе.
Скрубберы на основе известняка и извести
Мокрая очистка известняком и известью являются наиболее популярными коммерческими системами ДДГ.Присущая простота, доступность недорогого сорбента (известняк), производство полезного побочного продукта (гипса), надежность, доступность и высокая эффективность удаления (которая может достигать 99%) являются основными причинами эта популярность. Капитальные затраты обычно выше, чем у других технологий, таких как системы ввода сорбента; однако эта технология известна своими низкими эксплуатационными расходами, поскольку сорбент широко доступен, а система экономически эффективна.
Рис. 7.1 представляет собой общую схему, показывающую основные компоненты и компоновку, используемые для системы мокрого скруббера. Обратите внимание, что хранилище известняка, измельчитель и резервуар для хранения исходного шлама для производства известнякового шлама не показаны на рис. 7.1. Размер реакционного резервуара в этой системе должен обеспечивать достаточное время для осаждения компонентов серы и для растворения добавок.
7.1. Схематическая диаграмма типовых компонентов системы мокрого скруббера.
В мокром скруббере известняк/известь дымовой газ очищается 5–15% (по весу) взвесью солей сульфита/сульфата кальция вместе с гидроксидом кальция (Ca(OH 2 )) или известняком (CaCO 3 ).Гидроксид кальция образуется при гашении извести (CaO) в воде в соответствии с реакцией
[7. 1]CaOs+h3Ol→CaOH3s+тепло
известняк или гидроксид кальция перекачиваются в абсорбер распылительной колонны и впрыскиваются в него. Диоксид серы поглощается каплями суспензии, и в суспензии происходит ряд реакций. Реакции между кальцием и поглощенным диоксидом серы приводят к образованию соединений полугидрата сульфита кальция (CaSO4⋅12h3O) и дигидрата сульфата кальция (CaSO 4 · 2H 2 O).Оба эти соединения мало растворимы в воде и выпадают из раствора в осадок. Это усиливает поглощение диоксида серы и дальнейшее растворение известняка или гашеной извести.
Реакции, происходящие в скрубберах, сложны. Упрощенные общие реакции для скрубберов на основе известняка и извести: 32х3О1
для скруббера извести.
Полугидрат сульфита кальция можно превратить в дигидрат сульфата кальция при добавлении кислорода по реакции
[7.4]CaSO3⋅12h3Os+32h3Ol+12O2g↔CaSO4⋅2h3Os более сложными и включают в себя сочетание газожидкостных, твердожидкостных и жидкостно-жидкостных ионных реакций. В скруббере из известняка процесс описывают следующие реакции. В зоне газожидкостного контакта абсорбера (типичную схему системы известнякового скруббера см. на рис. 7.1) диоксид серы растворяется в водном состоянии
[7.5]SO2g↔SO21
и гидролизуется с образованием ионов водорода и бисульфата
[7.6]SO21+h3O1↔HSO3-+H+
Известняк растворяется в абсорбирующей жидкости с образованием ионов кальция и бикарбоната
[7.7] CaCO3s+H+↔Ca+++HCO3−
с последующей кислотно-щелочной нейтрализацией
[7.8]HCO3−+H+↔CO21+h3O1
отгонка CO 2 из шлама
[7.9] CO21↔CO2g
и растворение полугидрата сульфита кальция
[7.10]CaSO3⋅12h3Os↔Ca+++HSO3-+12h3O1
В реакторе скрубберной системы твердый известняк растворяется в водном состоянии (реакция [7.7]), происходит кислотно-основная нейтрализация (реакция [7.8 ]), CO 2 отгоняют (реакция [7.9]), а полугидрат сульфита кальция осаждают по реакции
[7. 11]Ca+++HSO3-+12h3O1↔CaSO3⋅12h3Os+H+ растворение сульфита кальция в зоне контакта газ-жидкость в абсорбере необходимо для того, чтобы свести к минимуму образование накипи полугидрата сульфита кальция в абсорбере (Wark et al., 1998). Равновесный pH для сульфита кальция составляет ≈ 6,3 при парциальном давлении CO 2 0,12 атмосферы, что является типичной концентрацией CO 2 в дымовых газах. Обычно рН поддерживают ниже этого уровня, чтобы предотвратить растворение полугидрата сульфита кальция (т. е. предотвратить протекание реакции [7.10] вправо).
Суспензия, возвращающаяся из абсорбера в реакционный резервуар, может иметь pH всего 3,5, который повышается до 5,2–6,2 путем добавления в резервуар свежеприготовленной известняковой суспензии (Wark et al., 1998). pH в реакционном резервуаре должен поддерживаться на уровне pH, который ниже равновесного pH карбоната кальция в воде, который составляет 7,8 при 77 °F.
Уравнения реакции для известкового скруббера аналогичны уравнениям для известнякового скруббера, за исключением того, что реакции [7. 7] и [7.8] заменены следующими реакциями соответственно (Stultz and Kitto, 1992)
[7.12] CaOH3s+H+↔CaOH++h3O1
[7.13]CaOH++H+↔Ca+++h3O1
Очистка известняком с принудительным окислением (LSFO) является одной из самых популярных систем на коммерческом рынке.Известняковая суспензия используется в открытой распылительной башне с окислением на месте для удаления SO 2 и образования гипсового шлама. Основными преимуществами этого процесса по сравнению с традиционной системой ДДГ из известняка (где продуктом является сульфит кальция, а не сульфат кальция (гипс)) являются более легкое обезвоживание шлама, более экономичная утилизация твердых продуктов скруббера и меньшее образование накипи на стены башни. LSFO способен удалить более 90% SO 2 (Radcliffe, 1991).
В системе LSFO горячий дымовой газ выходит из устройства контроля твердых частиц, обычно электростатического фильтра (ESP), и поступает в распылительную колонну, где он вступает в контакт с распыляемой разбавленной известняковой суспензией. SO 2 в дымовых газах вступает в реакцию с известняком в шламе посредством реакций, перечисленных ранее, с образованием полугидрата сульфита кальция. Через суспензию пропускают сжатый воздух, в результате чего этот сульфит естественным образом окисляется и гидратируется с образованием дигидрата сульфата кальция.Сульфат кальция может быть сначала обезвожен с помощью сгустителя или гидроциклонов, а затем обезвожен с помощью вращающегося барабанного фильтра. Затем гипс вывозится на свалку для утилизации. Образование кристаллов сульфата кальция в шламе рециркуляционного резервуара также помогает снизить вероятность образования накипи.
Абсорбирующий реагент, известняк, обычно подают в открытую распылительную колонну в виде водной суспензии при молярной скорости подачи 1,1 моль CaCO 3 /моль удаленного SO 2 .Этот процесс способен удалить более 90% SO 2 , присутствующего во входящем дымовом газе. Преимущества систем LSFO заключаются (Radcliffe, 1991) в следующем.
- •
На внутренних поверхностях башни меньше вероятность образования накипи из-за присутствия затравочных кристаллов гипса и пониженного уровня насыщения сульфатом кальция. Это, в свою очередь, позволяет повысить надежность системы.
- •
Гипсовый продукт фильтруется легче, чем сульфит кальция (CaSO 3 ), полученный с использованием обычных известняковых систем.
- •
В конечном утилизируемом продукте химическая потребность в кислороде ниже.
- •
Конечный продукт можно безопасно и легко утилизировать на свалке.
- •
Принудительное окисление позволяет использовать больше известняка, чем обычные системы.
- •
Сырье (известняк), используемое в качестве абсорбента, имеет низкую стоимость.
- •
LSFO легче модернизировать, чем системы естественного окисления, поскольку в этом процессе используется оборудование для обезвоживания меньшего размера.
Недостатком этой системы является высокая потребность в энергии из-за относительно более высокого отношения жидкости к газу, необходимого для достижения требуемой эффективности удаления SO 2 .
Конструкционные материалы
При работе мокрых скрубберов возникают две основные проблемы: коррозия и образование накипи на границе раздела «влажный-сухой»; эти проблемы можно свести к минимуму за счет использования специальных строительных материалов и ограниченного повторного использования растворов скрубберов. По мере увеличения уровня растворенных твердых веществ в известково-известняковой суспензии также увеличивается вероятность образования накипи.Если наблюдается избыточное образование накипи, большие перепады давления газа могут вызвать остановку.
pH рециркулируемого шлама обычно составляет от 5 до 6 в рециркуляционном резервуаре известняковой системы. Уровень pH в зоне распыления и на поддоне может составлять от 3,5 до 4. Концентрация хлоридов обычно рассчитана на уровне 20 000 частей на миллион по весу, но может достигать 100 000 частей на миллион, когда в качестве подпиточной воды используется морская вода. Конструкция из сплава (см. Таблицу 7.1) была наиболее популярным выбором поглощающих материалов в США (Kitto and Stultz, 2005).Модули скрубберов из углеродистой стали с резиновой футеровкой популярны в Европе.
Таблица 7.1. Некоторые сплавы для мокрой ДДГ (Kitto and Stultz, 2005)
Сплав | Cr: вес. % | Mo: вес. % | Ni: вес. Cl: PPM | |||||
---|---|---|---|---|---|---|---|---|
316 L | 16,0 | 2,0 907 | 10,0 | 0 | 0 | 10 000 | ||
20 | 19,0 | 2.0 | 32.0 | 32.0 | 0 | 12 000 | ||
317 L | 18.0 | 3.0 | 11,0 | 0 | 15 000 | |||
825 | 19.5 | 19.5 | 2,5 | 38,0 | 0 | 15 000 | ||
317LM | 18.![]() | 4.0 909 | 4.0 | 13,5 | 0 | 18 000 | ||
317LMN | 17,0 | 4,0 907 | 13.5 | 0,1 | 20 000 | |||
9001 | 4,0 904 | 40 9003 | 23.0 | 0 | ||||
2205 | 22,0 | 3.0 | 4,5 | 0,14 | 30 000 | |||
255 | ||||||||
255 | 255 | 29 0 | 2,9 | 45 | 0,1 | 45 000 | ||
G | 21.0 | 21.0 | 5.5 | 36,0 | 0 | 50 000 | ||
254-SMO | 19.5 | 6.0 | 6.0 | 17.5 | 0.18 | 55 000 | ||
Al-6xn | 20.0 | 20.0 | 6.0 | 0,18 | 55 000 | |||
625 | 20,0 | 8,0 | 58.![]() | 0 | 55 000 | |||
C-22 | 20,0 | 12,5 | 50,0 | 0 | 100 000 | |||
C-276 | 14,5 | 15.0 | 51.0 | 0 | 100 000 |
В промышленности используется ряд различных сплавов для корпуса абсорбера, поддона и внутренних опор. Также использовались резиновые покрытия, покрытия из чешуйчатого стекла и системы керамической плитки. Выбор материала для любого проекта зависит от химии процесса и анализа затрат и выгод материала с точки зрения жизненного цикла.
(PDF) Кристаллизация и фазовая стабильность CaSO4 и солей на основе CaSO4
[15] Wagman DD, Evans WH, Parker VB, Schumm RH, Halow I, Bailey SM, Churney KL, Nuttal
RL (1982) J Phys Chem Ref Data 11 Suppl No 2
[16] Knacke O, Gans W (1977) Z Phys Chem 104:41
[17] Barin I, Knacke O, Kubaschewski O (1977) Thermochemical Properties of Inorganic Sub-
позиций. В: Springer-Verlag Berlin, Heidelberg, New York
[18] Linke WF, Seidell A (1965) Solubilities of Inorganic and Metal Organic Compounds, 4th Ed,
Vol 1, 2, Amer Chem Soc, Washington DC
[19] Пельш А.Д. (1973) Справочник экспериментальных данных по растворимости в многокомпонентных водно-солевых
системах. Том 1 (1973), Том 2 (1975), Изд-во Химия, Ленинград,
[20] Marshall WL, Slusher R (1973) J Chem Thermodyn 5: 189
[21] Kalyanaraman R, Yeattts LB, Marshall WL (1973) ) J Chem Thermodyn 5: 891
[22] Крученко В.П., Беремжанов Б.А. (1980) Ж Неорг Хим 25: 3076
[23] Крученко В.П. (1985) Ж Неорг Хим 30: 1566
[24] Фрейер Д ( 2000) Zur Phasenbildung und -stabilit
€
AAT IM System NA
2
SO
4
-CASO
4
-H
2
O.Dis-
, TU Bergakademie Freiberg
[25] Monnin C (1990) Geochim Cosmochim Acta 54: 3265
[26] Monnin C (1999) Chem Geol 153: 187
[27] , Pitzer KS (1999) J Solution Chem 28: 667
[28] Mac Donald GJF (1953) Amer J Sci 251: 884
[29] Kr
€
uuger RR, Abriel W (1990) Z Naturforsch 45B: 1221
[30] Lancia A, Musmarra D, Prisciandaro M (1999) AIChE J 45: 390
[31] He S, Oddo JE, Tomson MB (1994) J Coll Interfac Sci 162: 297
[ 32] Prisciandaro M, Lancia A, Musmarra D (2001) AIChE J 47: 929
[33] Prisciandaro M, Lancia A, Musmarra D (2001) Ind Eng Chem Res 40: 2335
[34] He S, Oddo JE, Tomson MB (1994) J Coll Interfac Sci 163: 372
[35] Hina A, Nancollas GH (2000) In: Alpers ChN, Jambor JL and Nordstrom DK (ed) Reviews in
Mineralogy & Geochemistry; Сульфатные минералы, кристаллография, геохимия и экологическое значение. Минералогическое общество Америки, т. 40. Вашингтон, округ Колумбия, стр. 277
[36] De Vreugd CH, Witkamp GJ, van Rosmalen GM (1994) J Cryst Growth 144:70
[37] Liu ST, Nancollas GH (1975) ) J Colloid Interfac Sci 52: 593
[38] Kontrec J, Kralj D, Brececvic L (2002) J Cryst Growth 240: 203
[39] Boisvert JP, Domenech M, Foissy A, Persello J, Mutin JC ( 2000) J Cryst Growth 220: 579
[40] Bertoldi GA (1978) Zement-Kalk-Gips 31: 626
[41] Konak AR (1976) Krist Tech 11:13
[42] Amathieu L, Boistelle R (1987) Chem-IngTech 59: 858
[43] Badens E, Veesler St, Boistelle R (1999) J Cryst Growth 198=199: 704
[44] Follner S, Wolter A, Preusser A, Indris S , Silber C, Follner H (2002) Cryst Res Technol 37:
1075
[45] Solberg C, Hansen S (2001) Cem Concr Res 31: 641
[46] Conley RF, Bundy WM (1958) Geochim Космохим Акта 15:57
[47] Кушнир Дж. (1980) Геохим Cosmochim Acta 44: 1471
[48] Witkamp GJ, Rosmalen GM (1991) J Cryst Growth 108:89
[49] Curry NA, Jones DW (1971) J Chem Soc A: 3725
[50] Aslanian S , Stoilova D, Petrova R (1980) Z anorg allg Chem 465: 209
[51] Sakae T, Nagata H, Sudo T (1978) Am Mineral 63: 520
[52] Xu J, Butler IS, Gilson DFR (1999) Spectrochim Acta A55: 2801
[53] Rinaudo C, Lanfranco AM, Boistelle R (1996) J Cryst Growth 158: 316
[54] Hina A, Nancollas GH, Grynpas M (2001) J Cryst Growth 223 : 213
[55] Zdukos AT, Vaimakis TK (1985) Russ J Inorg Chem 30: 1124
[56] Haerter M (1971) Tonind-Ztg 95:9
[57] Ferraris G, Jones DW, Yerkess I (1971) Acta Cryst B27: 349
716 D. Freyer and W. Voigt
Влияние термической обработки на механические свойства и свойства деградации 3D-печатных каркасов на основе сульфата кальция
Трехмерная печать (3DP) использовалась для изготовления каркасов с преимуществами полностью контролируемой геометрии и воспроизводимости . В этом исследовании конструкция каркаса была установлена путем изучения минимального размера элемента и распределения размера порошка. Затем он был изготовлен из порошков на основе гипса 3DP (CaSO 4 ·1/2H 2 O).Каркасы, изготовленные из этого материала, продемонстрировали низкие механические свойства и высокую скорость деградации. В этом исследовании изучалось влияние термической обработки на механические свойства и свойства разложения in vitro каркасов CaSO 4 . Возникновение обезвоживания во время цикла нагрева привело к умеренному улучшению механических свойств и свойств деградации. При использовании протокола термообработки при 200°C в течение 30 мин прочность на сжатие увеличилась с 0,36 ± 0,13 МПа (предварительно термообработанная) до 2. 49 ± 0,42 МПа (термообработка). Термообработанные матриксы сохраняли свою структуру и компрессионные свойства до двух суток в трис-буферном растворе, тогда как необработанные матриксы полностью разрушались в течение нескольких минут. Несмотря на умеренные улучшения, наблюдаемые в этом исследовании, термообработанные каркасы из CaSO 4 не продемонстрировали механических свойств и свойств деградации, соответствующих требованиям для применения в области инженерии костной ткани.
1. Введение
Дефекты кости, превышающие критический размер, не могут быть излечены нормальными процессами ремоделирования кости и поэтому требуют замещения кости.Аутотрансплантат, признанный «золотым стандартом» восстановления кости, широко используется уже несколько десятилетий. Тем не менее, он по-прежнему имеет недостатки, в том числе риск передачи заболевания и ограниченную доступность по сравнению с постоянно растущим спросом на хирургическое вмешательство [1]. В США, например, ежегодно проводится более 0,5 млн хирургических вмешательств, связанных с восстановлением костей [2].
Одним из прорывов в инженерии костной ткани стала разработка трехмерных каркасов, которые заменяют и восстанавливают утраченные ткани.Они служат матрицей для посева клеток и переноса клеток в нужное место. Несмотря на первоначальный успех в разработке 3D-каркасов, в настоящее время перед исследователями стоит более сложная задача восстановления поврежденной кости в местах, несущих нагрузку [3]. Чтобы поддерживать функцию несущих костей, каркас должен обладать соответствующими механическими свойствами. Эти свойства сильно зависят от конструкции и геометрии лесов. Общий консенсус в отношении оптимальной конструкции каркаса, созданного из костной ткани, заключается в том, чтобы имитировать архитектуру, механические и биохимические свойства натуральной кости [4].Однако трудно контролировать геометрию каркасов с использованием традиционных методов изготовления каркасов, таких как литье растворителем/выщелачивание частицами, термическое фазовое разделение и репликация губки. Вместо того, чтобы создавать хорошо спроектированные каркасы, традиционные методы с большей вероятностью будут производить каркасы со случайной структурой [5].
Помимо этой движущей силы, в последнее время большое внимание уделяется методам свободной формовки твердых материалов (SFF). В отличие от традиционных методов изготовления строительных лесов, методы SFF позволяют создавать строительные леса, предварительно спроектированные с использованием 3D CAD / CAM (автоматизированное проектирование / автоматизированное производство).Можно изготавливать каркасы с полностью контролируемой геометрией и, следовательно, с заданными свойствами. Еще одним преимуществом использования методов SFF является высокая воспроизводимость, которая демонстрирует большой потенциал для клинического применения. Кроме того, компьютерная томография места дефекта генерирует компьютерные данные, на основе которых могут быть изготовлены воспроизводимые каркасы по индивидуальному заказу, точно отражающие форму дефекта [6].
Техника 3D-печати (3DP) является одной из наиболее изученных технологий SFF в производстве строительных лесов.3D-модели печатаются снизу вверх в порошковом слое. Гипс или полугидрат сульфата кальция (CaSO 4 · 1/2H 2 O) был одним из первых материалов, которые использовались для 3DP. Он может быть смочен коммерческим вяжущим (содержание воды 98%), а затем образует гипсовую пасту (CaSO 4 · 2H 2 O) путем активации самогидратации [7] посредством химической реакции (1) образуя гипсовую пасту (CaSO 4 ·2H 2 O). Порошок на основе CaSO 4 является одним из немногих материалов, имеющихся в продаже при производстве 3DP.Материалы на основе CaSO 4 ранее использовались для заполнения костных дефектов в ненесущих приложениях [8–10]. Он зарекомендовал себя как эффективный заполнитель костных пустот как в исследованиях на животных [11], так и на людях [12–14]. Было показано, что имплантаты CaSO 4 не увеличивают степень воспалительной реакции после имплантации [11]; они способны обеспечивать основу для прикрепления остеобластов и легко резорбируются остеокластами [15].
В настоящее время материалы на основе CaSO 4 также используются в качестве добавки для включения в биокерамику и биополимеры в качестве наполнителя.Кроме того, включение CaSO 4 может помочь в адаптации свойств разложения, повышении размерной стабильности и снижении стоимости [16]. Однако биоматериалы на основе CaSO 4 не демонстрируют достаточных механических свойств для восстановления несущих костных дефектов, а также из-за своей быстрой скорости деградации CaSO 4 быстро теряет основную часть своей формы и механических свойств в виво . Эти недостатки препятствуют использованию этого материала для наращивания кости после болезни или травмы:
Обезвоживание путем термической обработки является наиболее распространенным методом улучшения его свойств.Лоумунконг и др. [17] сообщили, что термическая обработка может сделать гипсовый блок нерастворимым, тем самым сохранив структуру при погружении в воду. Механизм дегидратации CaSO 4 интенсивно описан [18, 19]. Молекулы воды в водном растворе CaSO 4 легко извлекаются при термической обработке. При различных режимах термообработки CaSO 4 можно обнаружить три безводных вида: первый ангидрит, γ -CaSO 4 , образуется при температуре от 130°C до 200°C.Его называют «растворимым ангидритом», потому что γ -CaSO 4 сохраняет высокую реакционную способность и способен регидратироваться обратно в полугидрат CaSO 4 [19]. При дальнейшем повышении температуры материал CaSO 4 продолжит превращение в β -CaSO 4 и α -CaSO 4 до абсолютной температуры плавления (~1450°C) [19]. Ангидрит, полученный при высокой температуре, имеет более низкую реакционную способность, чем γ -CaSO 4 .
Целью данного исследования была разработка каркасов CaSO 4 с использованием техники 3DP. Улучшение механических свойств и профиль деградации полученных в результате каркасов CaSO 4 исследовали путем использования термической обработки в различных условиях. Влияние температуры нагрева на процесс дегидратации CaSO 4 анализировали с помощью термогравиметрического анализа (ТГА) и рентгеноструктурного анализа (РФА).
2. Материалы и методы
2.1. Материалы
Порошок полугидрата сульфата кальция (ZP 102, Z Corporation, Великобритания) и связующее на водной основе (ZB 7, Z Corporation, Великобритания) были приобретены и использованы в 3D-принтере (Zcorp 310, Z Corporation, Великобритания). Размер частиц и распределение частиц по размерам в порошках 3DP CaSO 4 определяли с использованием двухлазерного анализатора частиц Sympatec HELOS/BF (Sympatec Limited, UK). Порошок сканировали в трех повторах, чтобы получить средние значения , , и , которые представляют 10%, 50% и 90% материала, соответственно, с меньшим размером частиц, чем это значение.
2.2. Проектирование и изготовление строительных лесов
Была спроектирована пористая цилиндрическая конструкция (диаметр = 18,0 мм и высота = 13,2 мм) (рис. 1). Каналы пор были на 100% связаны между собой и разветвлялись ортогонально, что давало трехмерную пористость. Пористая структура поддерживалась периферийным рукавом. Образцы 3DP с тремя различными размерами пор и распорок (0,8, 1,2 и 1,6 мм) были первоначально изготовлены для определения минимального размера элемента, который можно было бы производить стабильно.
Проект лесов с элементами минимального размера был преобразован в файл STL и импортирован на 3D-принтер.Трехмерная структура была разделена на двумерные слои толщиной 0,1 мм. Во время процесса 3DP область подачи сначала заполнялась порошком полугидрата сульфата кальция, а валик распределял слой порошка из области подачи в область сборки (рис. 2). Печатающая головка выборочно наносила капли связующего вещества в область построения. После того, как первый слой был полностью нанесен, валик возвращался в зону подачи, а затем наносил еще один слой порошка в зону построения. Эта процедура повторялась непрерывно, и на создание полного каркаса уходило около 40 минут. Несвязанные порошки внутри структуры временно действовали как опора для окружающих связанных порошков. Затем несвязанные порошки удаляли с помощью сжатого воздуха, а каркасы сушили при 73°С в течение 1 часа.
2.3. Протокол термообработки
Термическую обработку водного CaSO 4 проводили в печи (BCF 11/8, Elite Thermal System Lt, UK). Каркасы 3DP подвергали термообработке при различных температурах в диапазоне от 150°C до температуры Таммана (861°C). Температура Таммана относится к температуре спекания, которая определяется как половина абсолютной температуры плавления.Сообщалось, что температура Таммана CaSO 4 составляет 861°С [19]. Однако, когда температура нагрева была увеличена выше 250°C, каркас CaSO 4 претерпел значительное изменение цвета (рис. 3). Это изменение цвета не было очевидным для каркасов CaSO 4 , подвергнутых термообработке при 861°C; однако наблюдалась большая деформация конструкции каркаса.
Поэтому для дальнейшего исследования были выбраны температуры 150°C, 200°C и 250°C. Все процессы нагрева начинали при комнатной температуре со скоростью нагрева 10°С/мин. Также были исследованы два разных времени пребывания при целевой температуре (30 мин и 1 ч). Затем оценивали влияние температуры нагрева и времени выдержки на процесс дегидратации CaSO 4 . Каркасы 3DP, подвергнутые термообработке при различных температурах, измельчали в порошок с помощью пестика и ступки для последующего рентгеноструктурного анализа (XRD), проводимого с использованием дифрактометра Philips X’ Pert PRO (PANalytical UK, Кембридж, Великобритания).Результаты были проанализированы с использованием программного обеспечения Phillips X’ Pert High Score Software (PANalytical Ltd, Великобритания). Потеря массы материала CaSO 4 после термообработки также определялась с помощью термогравиметрического анализа (ТГА). Порошок CaSO 4 помещали в аппарат NETZSCH STA 449 C Jupiter (NETZSCH-Geratebau GmbH, Германия) и нагревали от 25°С до 300°С со скоростью 10°С/мин, что соответствовало полной термообработке.
Процесс, которому подвергались леса.
Блоки тех же размеров, что и подмости (диаметр = 18.0 мм и высотой = 13,2 мм) были изготовлены с использованием 3DP. Затем они подвергались той же термической обработке, что и каркасы. Измеряли потерю массы как блоков, так и каркасов, а затем сравнивали с теоретической потерей массы при полной дегидратации из водного CaSO 4 в ангидрит.
2.4. Испытание на сжатие
Свойства каркасов на сжатие были измерены с использованием универсальной системы испытаний материалов (EZ50, Lloyds Instruments, Великобритания) с тензодатчиком 5 кН и при скорости смещения 0.5 мм/мин. Всего было протестировано четыре каркаса для каждого условия. Было определено, что образец вышел из строя, когда нагрузка в постпиковой области снизилась до 80% от пиковой нагрузки. Прочность на сжатие определяли как максимальную зарегистрированную нагрузку, деленную на начальную площадь поперечного сечения каркаса. Модуль сжатия определяли путем измерения максимального наклона упругой области кривой зависимости напряжения от деформации непосредственно от области схождения. Правило Симпсона использовалось для расчета ударной вязкости при сжатии, которая обозначалась как площадь под кривой зависимости напряжения от деформации при сжатии до точки разрушения.
2.5. Свойства разложения
Были исследованы свойства разложения in vitro каркасов CaSO 4 до и после термообработки (т.е. температура спекания 200°C и время выдержки 30 мин). Каждый каркас взвешивали, а затем погружали в забуференный раствор трис-HCl с pH 7,4 (37°C, 100 мл). Трис имеет полное название трис(гидроксиметил)аминометан и представляет собой химическое соединение, которое регулярно используется в качестве буфера из-за его низкой стоимости и способности поддерживать уровень pH между 7 и 9 за счет поглощения противоионов ( и ).В каждый заданный момент времени (1, 2, 4 и 7 дней) из буферного раствора удаляли по три каркаса каждой группы. Размерные изменения были измерены сразу после удаления. Каркасы промывали деионизированной водой и сушили в печи при 37°C в течение 48 часов. Затем измеряли сухую массу для расчета изменения массы до и после погружения в буферный раствор. Компрессионные свойства каждого каркаса были определены в соответствии с разделом 2.4.
2.6. Статистический анализ
Данные, собранные во время всех экспериментальных тестов, оценивали на статистическую значимость с использованием однофакторного дисперсионного анализа (ANOVA) с последующим апостериорным тестом HSD Тьюки для сравнения между каждой группой.Значение считалось существенно отличающимся. Данные, которые были примерно нормально распределены, были определены на основе тестов нормальной вероятности. Тесты проводились с использованием студенческого программного обеспечения Minitab 14 (Minitab, Inc., США) и программного обеспечения SPSS 13.0 (SPSS, США).
3. Результаты и обсуждение
3.1. Конструкция каркаса и размер порошка 3DP
Четко определенные каркасы были изготовлены с использованием метода 3DP для каждой из протестированных конфигураций размеров пор и распорок (т. 8, 1,2 и 1,6 мм). После изготовления каждая из конструкций лесов обладала достаточной прочностью в неспеченном состоянии, чтобы выдерживать давление пневматического пистолета при удалении несвязанного порошка. Однако было трудно удалить весь несвязанный порошок. Однако было трудно удалить весь несвязанный порошок с каркаса с наименьшим размером элемента 0,8 мм. Поэтому минимальный размер элемента, который был выбран для конструкции каркаса, составлял 1,2 мм. Взаимосвязь между оптимальным размером пор каркаса и клеточной активностью всегда вызывала споры в литературе [20].Большие поры (> 0,5 мм) способствуют быстрой васкуляризации, но также уменьшают удельную площадь поверхности, что ограничивает прикрепление клеток [21]. Это представляет собой потенциальное ограничение технологии 3DP из-за сложности удаления несвязанного порошка из небольших полостей внутри каркаса после изготовления. Плазменная обработка частиц порошка может предложить потенциальное решение для повышения текучести порошка [22].
Обеспыливание также может быть более эффективным, если порошок предварительно нагревается, чтобы устранить его воздействие влаги.Преимущество порошка с относительно небольшим размером частиц состоит в том, что его легко удалить, но он склонен к агломерации в порошковом слое [22]. Коммерческий порошок ZP102 был обработан до соответствующего размера частиц порошка ( мкм, мкм, рис. 4) для 3DP, что позволило избежать агломерации. Кроме того, этот размер частиц порошка ограничивал минимальный размер элемента, особенно в случае изготовления сложной сотовой структуры в этом исследовании. Размер частиц порошка также влияет на толщину слоя, которую можно получить.Тонкие слои порошка предпочтительнее, так как может быть достигнуто относительно более высокое разрешение, но также предполагается, что слои должны быть толще, чем наибольший размер частиц порошка. Принимая во внимание все необходимые факторы, в качестве толщины слоя для данного исследования была выбрана 100 мкм, так как используемые частицы порошка имели мкм.
3.2. Влияние термической обработки на CaSO
4 Дегидратация Имеющийся в продаже порошок 3DP состоит в основном из полугидрата сульфата кальция и небольшого количества водорастворимых органических добавок, которые способствуют связыванию частиц порошка во время печати.Присутствие этих добавок может ограничить температуру, которая может воздействовать на каркасы во время термообработки, поскольку может произойти разложение. Изменение цвета каркасов, которое было очевидно после термической обработки, свидетельствовало о присутствии органических компонентов в коммерческом порошке ZP102, использованном в этом исследовании. В предыдущих исследованиях для связывания гипсового порошка 3DP во время 3DP использовались мальтодекстрин и сахар (Plaster Powder V2, онлайн, 26 мая 2012 г.), что может привести к значительному разложению готовых отпечатанных образцов при нагревании выше 250°C.Однако точные добавки, используемые в коммерческом порошке 3DP, остаются неизвестными из-за коммерческой тайны. Некоторые исследователи предположили, что изменение цвета, наблюдаемое после термообработки, может быть связано с нагретым глицерином, который был обнаружен в рецептурах коммерческих связующих [17]. В этом исследовании органические компоненты подверглись значительному разложению, когда каркасы подвергались термообработке при температурах выше 250°C. Чтобы уменьшить степень органического разложения, температура, используемая в процессе термообработки, не поднималась выше 250°C в этом исследовании.
Рентгенодифракционный анализ каркасов до термообработки показал пики, характерные для дигидрата CaSO 4 (рис. 5). Это показало, что во время процесса 3DP гипсовые порошки полугидрата CaSO 4 реагировали со связующим на водной основе и превращались в дигидраты. После термообработки при 150°С значительная часть пиков дигидрата CaSO 4 исчезла. Однако процесс дегидратации не завершался при 150°С, на что указывало наличие некоторых затухающих пиков дигидрата CaSO 4 . Все характерные пики для дигидрата CaSO 4 исчезали при повышении температуры до 200°C, что свидетельствовало о полном извлечении молекул воды из водного порошка CaSO 4 . Отчетливых различий между рентгенограммами порошков, термообработанных при 200°С и 250°С, не наблюдалось.
Дегидратация CaSO 4 начинается с начала цикла нагревания, как показано с помощью ТГА (рис. 6). Было замечено, что на первом этапе обезвоживания скорость потери массы была относительно низкой.Эта ранняя дегидратация была связана с потерей свободно удерживаемой цеолитовой воды до более поздней потери решеточной воды [23]. Это соответствовало другим исследованиям, в которых дегидратация CaSO 4 была медленной при температуре ниже 95°C, а затем ускорялась между 95°C и 170°C [24]. В данном исследовании в том же диапазоне температур (95–170 °С) наблюдался значительный процесс дегидратации. Изменение массы, связанное с превращением CaSO 4 ·2H 2 O в β -CaSO 4 ·1/2H 2 O и β -CaSO 3 4 1/2H194 2 O до γ -CaSO 4 [23]. Первым безводным веществом, полученным во время цикла нагревания, был γ -CaSO 4 . Полное образование γ -CaSO 4 наблюдалось при 196,9°С. Кривая ТГА начала выходить на плато при этой температуре. Результаты ТГА подтвердили рентгенограммы, которые показали, что полная дегидратация CaSO 4 была достигнута примерно при 200°C. На третьей стадии (от 200°C до 250°C) значительных превращений обнаружено не было, так как была зарегистрирована только потеря массы 0,3%.Преобразование γ -CaSO 4 в другие безводные соединения началось приблизительно при 250°C. Потеря массы при температуре выше 250°C также может быть связана с разложением органических добавок в коммерческом порошке 3DP.
XRD и ТГА показали, что дегидратация CaSO 4 завершилась примерно при 200°C. После термообработки при 200°С в течение 30 мин потеря массы блоков 3ДП составила 11,4% от исходной массы (рис. 7). Теоретическая потеря массы при полной конверсии CaSO 4 · 1/2H 2 O и CaSO 4 · 2H 2 O в CaSO 4 составляет приблизительно 5% и 20% соответственно. Таким образом, порошок CaSO 4 ·1/2H 2 O частично смачивался связующим на водной основе во время процесса 3DP. Детали 3DP должны иметь химическую формулу CaSO 4 · n H 2 O (). Однако рассчитать точное значение n было затруднительно из-за небольшой доли добавок в коммерческом порошке CaSO 4 ·1/2H 2 O. Сообщалось, что примеси могут оказывать значительное влияние на величину потери массы [25]. Этот результат был адаптивным к каркасам 3DP, поскольку не было существенной разницы в потере массы между блоками и каркасами (-значение> 0.05).
3.3. Влияние термической обработки на свойства сжатия
CaSO 4 ·H 2 Каркасы O, не подвергнутые термической обработке, продемонстрировали низкую прочность на сжатие, модуль сжатия и ударную вязкость (рис. 8). Прочность на сжатие (0,36 ± 0,13 МПа), например, была значительно ниже, чем у губчатой кости (4–12 МПа) [3]. Сообщалось, что прочность на растяжение, удлинение и ударная вязкость с надрезом снижались, когда PLA был сильно наполнен гипсом [16].
После термической обработки компрессионные свойства каркасов из CaSO 4 резко возросли. Прочность на сжатие значительно увеличилась с 0,36 ± 0,13 МПа (предварительно термообработанная) до 2,49 ± 0,42 МПа (термообработка при 200°C в течение 30 мин), модуль сжатия также значительно увеличился с 4,98 ± 1,17 МПа (предварительно нагретая после обработки) до 28,81 ± 3,07 МПа (термообработка при 200°C в течение 30 мин) (значение <0,05). Улучшение свойств при сжатии показало, что безводный CaSO 4 показал лучшие механические характеристики по сравнению с его водным аналогом.В результате обезвоживания первый ангидрит преобразовывался между 90°С и 200°С, что способствовало улучшению механических свойств.
Наблюдение за сжимающими кривыми зависимости напряжения от деформации (рис. 9) показало, что строительные леса сначала подверглись упругому смещению, за которым последовала постоянная пластическая деформация, вызванная образованием вышедших из строя распорок и микротрещин в периферийной втулке строительных лесов. Термическая обработка каркасов при 200°С привела к увеличению модуля сжатия, а область пластичности расширилась, что свидетельствует о более высокой ударной вязкости.Напротив, каркасы, прошедшие термообработку при 250°С, демонстрировали более низкий уровень пластической деформации и, как правило, разрушались вскоре после достижения пиковой нагрузки. Таким образом, была получена сильная корреляция между степенью обезвоживания и механическими свойствами. Наибольшее улучшение прочности на сжатие (692%), модуля сжатия (579%) и ударной вязкости (700%) было достигнуто при нагревании каркасов при 200°C в течение 30 мин. Рентгенодифракционная дифракция и ТГА показали, что температура, при которой CaSO 4 достигает полной дегидратации, составляет приблизительно 200°C.Однако при повышении температуры термообработки с 200°С до 250°С наблюдалась тенденция к снижению компрессионных свойств. Предполагается, что снижение компрессионных свойств частично связано с разложением органических добавок при температурах ≥250°C.
Каркасы 3DP, термообработанные при 250°C, продемонстрировали значительное снижение ударной вязкости и стали более хрупкими, чем каркасы, термообработанные при более низких температурах (рис. 8). Продолжительность цикла термообработки также играла важную роль.По сравнению с циклом термообработки продолжительностью 1 час, термообработка в течение 30 минут показала превосходные свойства сжатия. Таким образом, степень органического разложения зависела как от температуры, так и от времени. Таким образом, следует избегать перегрева CaSO 4 при выборе оптимальной температуры нагрева и времени выдержки. Наивысшие компрессионные свойства каркасов из CaSO 4 были достигнуты при соблюдении протокола термообработки при 200°C в течение 30 мин.
3.4. Влияние термической обработки на свойства разложения
Погружение каркаса CaSO 4 · n H 2 O в трис-буферный раствор привело к полному растворению менее чем за 10 мин (рис. 10). Предыдущие исследования показали, что CaSO 4 · n H 2 O имеет высокую скорость растворимости [17]. Из-за быстрой деградации предварительно термообработанных каркасов CaSO 4 · n H 2 O компрессионные свойства этой группы определить не удалось.
Также были определены свойства деградации термообработанных каркасов (200°C в течение 30 мин). Рентгенофазовый анализ и ТГА показали, что гипс полностью потерял свои молекулы воды и превратился в ангидрид при температуре приблизительно 200°C. Однако этот процесс обезвоживания обратим, то есть может произойти регидратация.
Гипс (CaSO 4 ·2H 2 O) = полугидрат (CaSO 4 ·0,5H 2 O) = растворимый ангидрит (CaSO 4 ) [18].
Было замечено, что термообработанные каркасы набухали при погружении в трис-буферный раствор (рис. 10). Средняя высота увеличилась на 25,0% (1-й день) и 28,8% (2-й день), а средний диаметр увеличился на 17,2% (1-й день) и 21,7% (2-й день) (рис. 11). Размерное расширение каркасов было связано с реконверсией растворимого ангидрита в водный CaSO 4 . Материал увеличивался в массе на протяжении всего процесса регидратации, что подтверждается незначительным увеличением сухой массы в день 1 (0,001).8%) и день 2 (0,9%) (рис. 11), что затрудняет определение скорости деградации. Каркасы, подвергнутые термообработке, сохранили большую часть своей структуры в течение первых двух дней деградации (рис. 10). Из-за этого процесса регидратации было трудно определить скорость деградации каркасов. Несмотря на увеличение массы, механические свойства снизились. Термообработанные каркасы из CaSO 4 продемонстрировали компрессионные свойства на 2-й день, которые более чем вдвое превышали уровень, зафиксированный в 0-й день (рис. 12).Это было значительным улучшением по сравнению с матриксами, не подвергавшимися термообработке (значение <0,05).
Термообработанный CaSO 4 каркасы подверглись in vitro деструкции от наружной поверхности внутрь, что вызвало большую деформацию периферического рукава конструкции каркаса. На 2-й день на внешнем рукаве каркасов CaSO 4 наблюдались небольшие насечки, что свидетельствует о начале процесса растворения.Впоследствии термообработанные каркасы CaSO 4 продемонстрировали значительное снижение структурной целостности между 2-м и 4-м днями. Следовательно, большие изменения и снижение размеров, массы и свойств сжатия были зарегистрированы на 4-й день. Между 4-м днем и 4-м днем 7, каркасы CaSO 4 подверглись дальнейшему растворению и деградации, что очень затрудняет получение каких-либо количественных данных после 4-го дня.
3.5. Ограничения и дальнейшая работа
Несмотря на умеренные улучшения как свойств сжатия, так и свойств разложения in vitro каркасов на основе 3DP CaSO 4 , которые были зарегистрированы в этом исследовании, также были отмечены ограничения.Во-первых, свойства как на сжатие, так и на деградацию in vitro не соответствовали требованиям, предъявляемым к матриксам, используемым в инженерии костной ткани. Было высказано предположение, что механические свойства костных каркасов должны имитировать свойства губчатой кости, демонстрируя прочность на сжатие от 4 до 12 МПа [3]. Скорость деградации каркасов также должна совпадать со скоростью образования новой кости, для завершения которой обычно требуется несколько месяцев для костной ткани. Поэтому до тех пор, пока эти свойства не могут быть существенно улучшены с помощью альтернативных стратегий, дальнейшие исследования в том же направлении следует проводить с осторожностью.Потенциальные альтернативные подходы могут включать введение биорезорбируемого полимера (полимолочной кислоты или поликапролактона) с инфильтрацией матрицы CaSO 4 в структуру или покрытие поверхности. Во-вторых, используемый коммерческий гипсовый порошок 3DP содержит относительно небольшое количество органической добавки, что может представлять проблему биосовместимости, поскольку состав этого материала остается неизвестным. В будущих исследованиях следует рассмотреть возможность использования более чистого материала CaSO 4 .
Поскольку отсутствие добавки может снизить реакционную способность между порошком и связующим, включение одобренного FDA материала (например, мальтодекстрина) в чистый CaSO 4 может оказаться жизнеспособной альтернативой. Наконец, применение водорастворимого полимера может быть целесообразным в качестве потенциального связывающего агента, так как он может сгорать при высокой температуре.
4. Заключение
Это исследование показало, что применение подходящего протокола термообработки может улучшить механические свойства и свойства разложения in vitro каркасов на основе 3DP CaSO 4 .Улучшенные свойства были следствием процесса обезвоживания, происходившего при термообработке. Несмотря на этот факт, термообработанные каркасы из CaSO 4 продемонстрировали умеренное улучшение характеристик сжатия и скорости деградации, что считается неприемлемым для применения в области инженерии костной ткани. В целом, результаты этого исследования выявили не только потенциальную возможность использования каркасов на основе 3DP CaSO 4 , но и предполагаемые ограничения. Были предложены альтернативные стратегии в попытке улучшить производство и применимость костных каркасов на основе 3DP CaSO 4 .
Раскрытие информации
Авторы этого документа не имеют прямых финансовых отношений или соглашений с коммерческими компаниями, указанными в этом документе. Таким образом, ни у кого из авторов не существует конфликта интересов в отношении содержания данной статьи.
Энергии | Бесплатный полнотекстовый | Влияние температуры обжига синтетического гипса на гранулометрический состав и время схватывания модифицированных строительных материалов
3.1. Результаты гранулометрического состава
Все исследованные образцы строительных материалов характеризовались хорошей смачиваемостью. При экспериментальных испытаниях во всех случаях мощность насосов использовалась на 60 %, а мощность света и ультразвука на 100 %. В первые 10 с измерений пузырьки воздуха удалялись, а время добавления каждого образца в диспергирующую часть прибора составляло не более 30 с. Каждый гипсовый материал измеряли трижды.

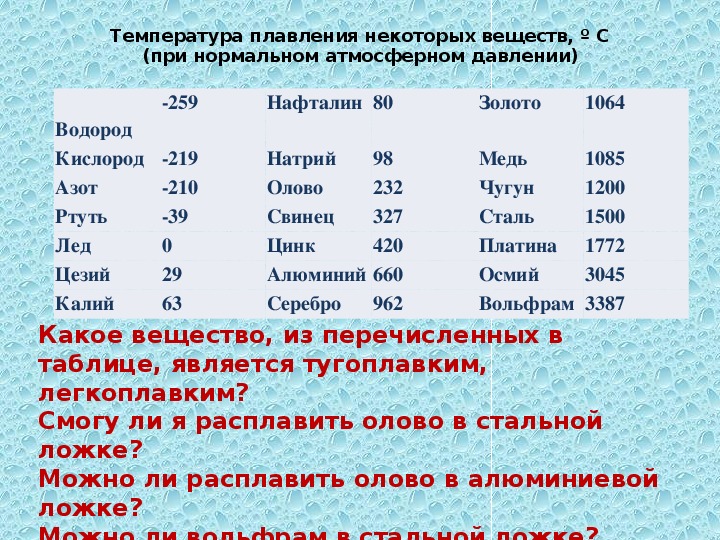
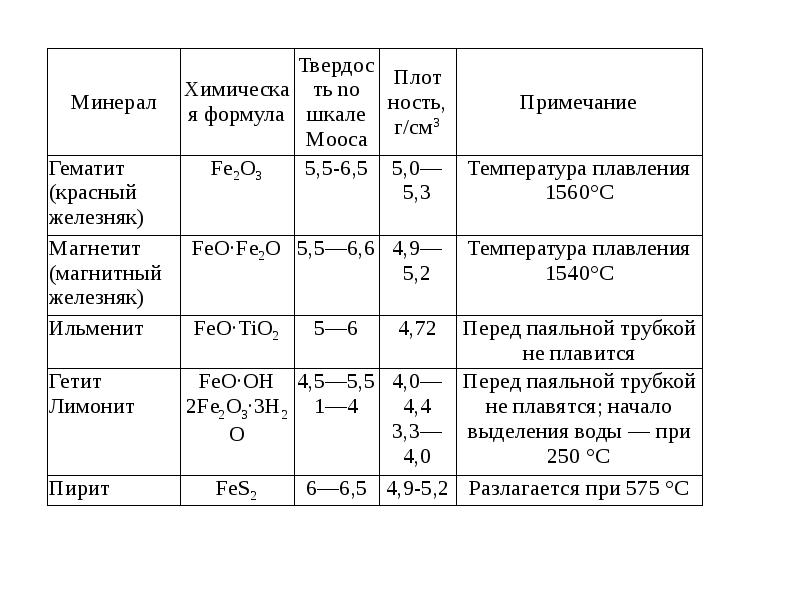
φave(d)=A⋅ln(d)+B
(10)
где A и B — постоянные значения уравнения.Во всех случаях получена очень хорошая совместимость экспериментальных результатов с предложенной зависимостью (10), что подтверждается высокими значениями параметра R 2 (табл.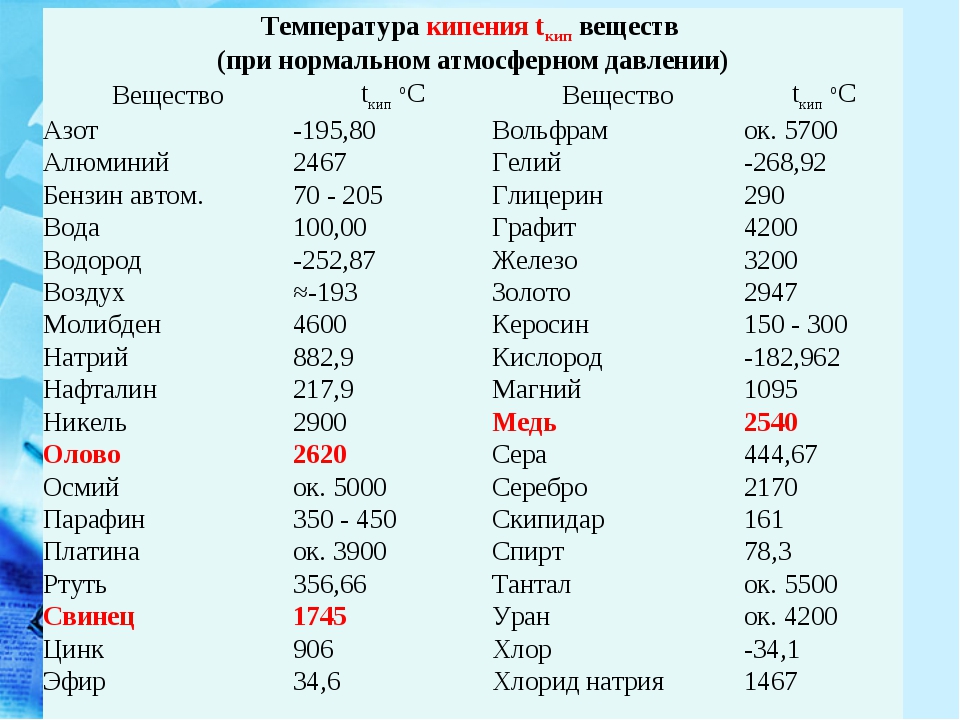
3.2. Результаты определения сроков схватывания гипсовых масс и кладочных и штукатурных растворов
Для предложенных составов гипсовых масс (табл. 4) были проведены замеры сроков их схватывания по температуре обжига синтетического гипса (рис. 9). В случае замеров времени схватывания образцов модифицированного гипса они проводились трижды для образца из одних и тех же гипсовых масс.Результаты по времени связывания были идентичными, поэтому статистические расчеты не проводились. Пасты из гипса, полученные в процессе обжига при 170 и 180 °C, имеют более длительное время схватывания. Более высокая температура обжига гипса сокращала время схватывания. В процессе связывания первичные гидраты постепенно возникали в виде мелких кристаллов (зародышей кристаллизации). Чем больше степень их проявления, тем больше скорость образования новых зародышей кристаллизации.Пасты с содержанием гипса, полученные при более высоких температурах обжига, вероятно, содержали повышенное количество кристаллизационных зародышей, что ускоряло процесс схватывания. Сомнения были бы однозначно развеяны при использовании фотографий, полученных с помощью сканирующего электронного микроскопа (СЭМ), однако они не являются предметом данной публикации. Такой анализ следует проводить в дальнейшем на уровне микроструктуры образцов.
t p = — 0,08 T + 20,4
(11)
т к = — 0,26 Т + 58,5
(12)
Было замечено, что время схватывания сокращалось с увеличением температуры обжига сырого гипса (рис. 10). Для гипса, прокаленного при 170 °С, начало схватывания начинается на 7-й минуте процесса схватывания и завершается на 14-й минуте. Однако для гипса, прокаленного при 190 °С, эти времена составили 5,5 и 9 мин соответственно. Важно также, что весь процесс схватывания сокращался при повышении температуры обжига гипса.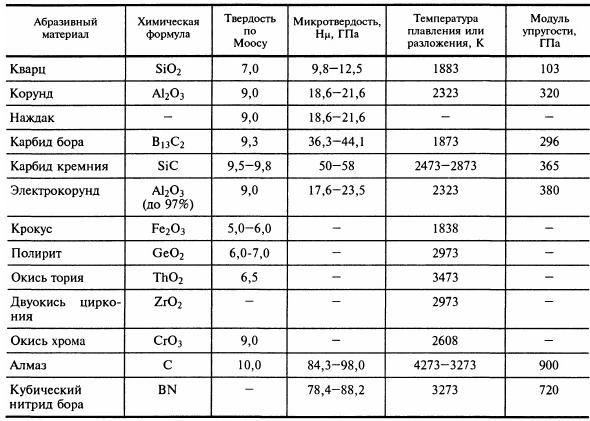

Дополнительным испытанием, не включенным в стандарты, было определение времени удобоукладываемости растворов. Параметром является время, в течение которого раствор еще не начал схватываться, и поэтому он показывает способность легко и точно заполнять формы, сохраняя при этом однородность. За это время можно нанести его на стену и внести любые исправления, возникшие в результате ошибок, возникших при строительных работах.Это очень важная характеристика свежих гипсовых растворов, которая отражается на качестве уже затвердевших композитов и изделий из них.
На Рисунке 11 и Рисунке 12 дополнительно представлена взаимосвязь между временем схватывания и удобоукладываемостью кладочных и штукатурных растворов, модифицированных винной кислотой и Plast Ret, в зависимости от температуры обжига синтетического гипса. На рисунках отмечено расчетное значение 5% погрешности. При сравнении времени схватывания кладочных растворов было показано, что все растворы, содержащие синтетический гипс и Plast Retard, имели более длительное время удобоукладываемости по сравнению с раствором на основе строительный гипс.
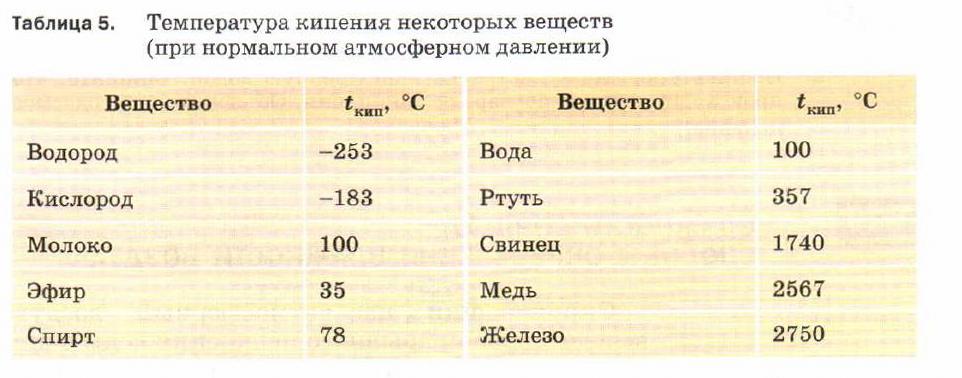
На вышеуказанные параметры сильно влияет pH раствора. Было замечено, что рН раствора влияет на прочность материалов, а коэффициент замедления не имеет прямого отношения к прочности полученных композитов. Показано, что морфология затвердевшего гипсового гипса в значительной степени зависит от значения рН воды и добавленного замедлителя схватывания, а максимальная прочность на сжатие достигается при рН равном 7. 90–113 В последние годы Многие исследовательские центры изучали влияние следующих химических соединений на время схватывания: винная кислота, виннокислый натрий, салициловая кислота, меламин, сахароза, белый цемент, трифосфат натрия, лимонная кислота, черный чай и полифосфат натрия [12,13]. ,57,58].Результаты их работы показали, что все виды замедлителей схватывания по-разному влияли на строительный гипс, и в то же время все они по-разному влияли на прочность гипса. В работе [14] представлено исследование влияния композиционной модифицирующей добавки. , в состав которого входят гашеная известь и суперпластификатор, на прочностные свойства и специфику формообразования структуры вяжущего. Прочность на сжатие образцов из модифицированных вяжущих составила от 20 до 24 МПа, а на изгиб от 10 до 12 МПа через 28 сут.Прочностные испытания строительных материалов на основе модифицированного гипса очень важны с точки зрения инженеров-строителей. В настоящее время авторы данной публикации планируют исследования прочности гипсовых материалов на основе синтетического гипса, полученного сероочисткой дымовых газов. В свою очередь авторы работы [59] проанализировали влияние теплоизоляционного материала на энергетическую и экологическую эффективность. здания. Здание было построено с учетом принципов устойчивого развития, как с точки зрения его дизайна, так и технических решений.Для оценки влияния теплоизоляционного материала были рассмотрены различные конфигурации перегородок, а исходный материал (стекловата) был заменен на синтетические (пенопласт, полистирол) и натуральные материалы (древесное волокно и кенаф).
Более того, авторы [60] внесли усовершенствования в деревянные конструкции по следующим параметрам: комфорт использования, энергосбережение или, шире говоря, устойчивое развитие. В связи с работами [59, 60] целесообразно провести испытания перегородок из материалов на основе синтетического гипса (предложенных в данной статье) на их термические и механические свойства.Более совершенные строительные технологии позволяют добавлять в гипс фотокатализаторы, например, TiO 2 , для получения самоочищающегося строительного материала и материала с высокими фотокаталитическими свойствами [61].
Важным аспектом, помимо механических свойств, является поиск композитов с низкими значениями теплопроводности. Очень часто улучшение термических свойств ухудшает механические свойства материалов. Большой проблемой для ученых является получение материала с очень хорошими механическими и термическими свойствами.
В настоящее время в строительной отрасли наблюдается тенденция поиска новых альтернатив традиционным функциональным добавкам для гипса.